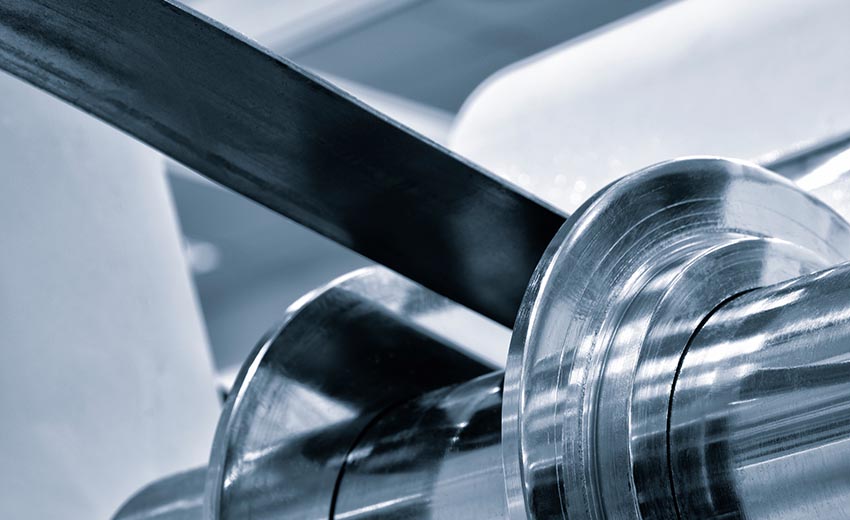
Introduction to Cold Roll Forming
Cold roll forming is a cost-effective metal forming process that involves shaping a long strip of metal sheet into a desired cross-sectional profile by passing it through a series of rolls. This process is widely used in various industries to manufacture components with complex shapes and excellent dimensional accuracy. To achieve the best results in cold roll forming, it is essential to consider several key design principles and best practices.
Design Considerations for Cold Roll Forming
Material Selection
Choose the appropriate material based on the requirements of the final product. Consider factors such as strength, ductility, and formability. Commonly used materials in cold roll forming include steel, aluminum, and stainless steel.
Cross-Sectional Profile
Design the cross-sectional profile of the part with consideration for its functionality, structural integrity, and ease of manufacturing. Optimize the design for material usage to reduce waste and improve cost-effectiveness.
Bend Radii and Corner Radii
Maintain uniform bend radii and corner radii throughout the design to avoid material thinning and deformation. Use larger radii in areas with complex shapes to prevent cracking and improve formability.
Thickness and Tolerance
Specify the appropriate material thickness and dimensional tolerances to meet the required strength and dimensional accuracy of the final product. Consider the capabilities of the cold roll forming process when defining tolerances.
Best Practices for Cold Roll Forming
Minimise Material Waste
Design parts with optimized material usage to minimize waste and reduce production costs. Utilize nesting software to layout parts efficiently on the raw material sheet.
Symmetry and Balance
Incorporate symmetry and balance into the design to ensure uniform deformation during the cold roll forming process. Symmetrical parts are easier to form and result in better quality products.
Avoid Sharp Corners
Eliminate sharp corners in the design to prevent material thinning, cracking, and distortion during cold roll forming. Use fillets and radii to distribute stress evenly and improve formability.
Consider Pre- and Post-Processing
Plan for any pre- or post-processing operations required to achieve the desired surface finish, dimensional accuracy, or functionality of the part. Coordinate these processes with the cold roll forming operation to streamline production.
Conduct Simulation and Testing
Use modeling and simulation tools to analyze and optimize the cold roll forming process before production. Conduct physical testing to validate the design and ensure conformance to specifications.
Collaborate with Suppliers
Work closely with cold roll forming suppliers to leverage their expertise and experience in metal forming. Collaborate on design reviews, process optimization, and quality assurance to achieve the best results.
Conclusion
Designing for cold roll forming requires careful consideration of material selection, cross-sectional profile, bend radii, and tolerances. By following best practices such as minimizing waste, maintaining symmetry, avoiding sharp corners, and collaborating with suppliers, you can optimize the design for cold roll forming and achieve high-quality products. Incorporate these principles into your design process to ensure success in cold roll forming applications.
This design guide provides a foundation for creating efficient and effective cold roll forming designs, helping you to leverage the benefits of this versatile metal forming process.