With over 40 years of experience, our expertise in producing custom profiles and rings exceeds industry standards for quality. We handle material thicknesses from 0.25mm to 3mm and strip widths up to 250mm. Our capabilities also extend to ring diameters ranging from 100mm to 2 meters. Most importantly, we prioritise building lasting relationships with our customers to ensure their continued satisfaction and loyalty.
What is (cold) roll-forming?
Cold roll forming is a manufacturing process used to shape metal sheets or coils into desired profiles or shapes at room temperature. Unlike hot rolling, which involves heating the metal, cold roll forming utilises a series of rollers to gradually bend and form the material without altering its properties.
This method is commonly used in industries such as construction, automotive, and aerospace to create products like beams, channels, tubes, and panels with high precision and consistency. Cold roll forming offers advantages such as cost-effectiveness, material efficiency, and the ability to produce complex geometries with tight tolerances, making it a versatile and widely adopted technique in the metalworking industry.
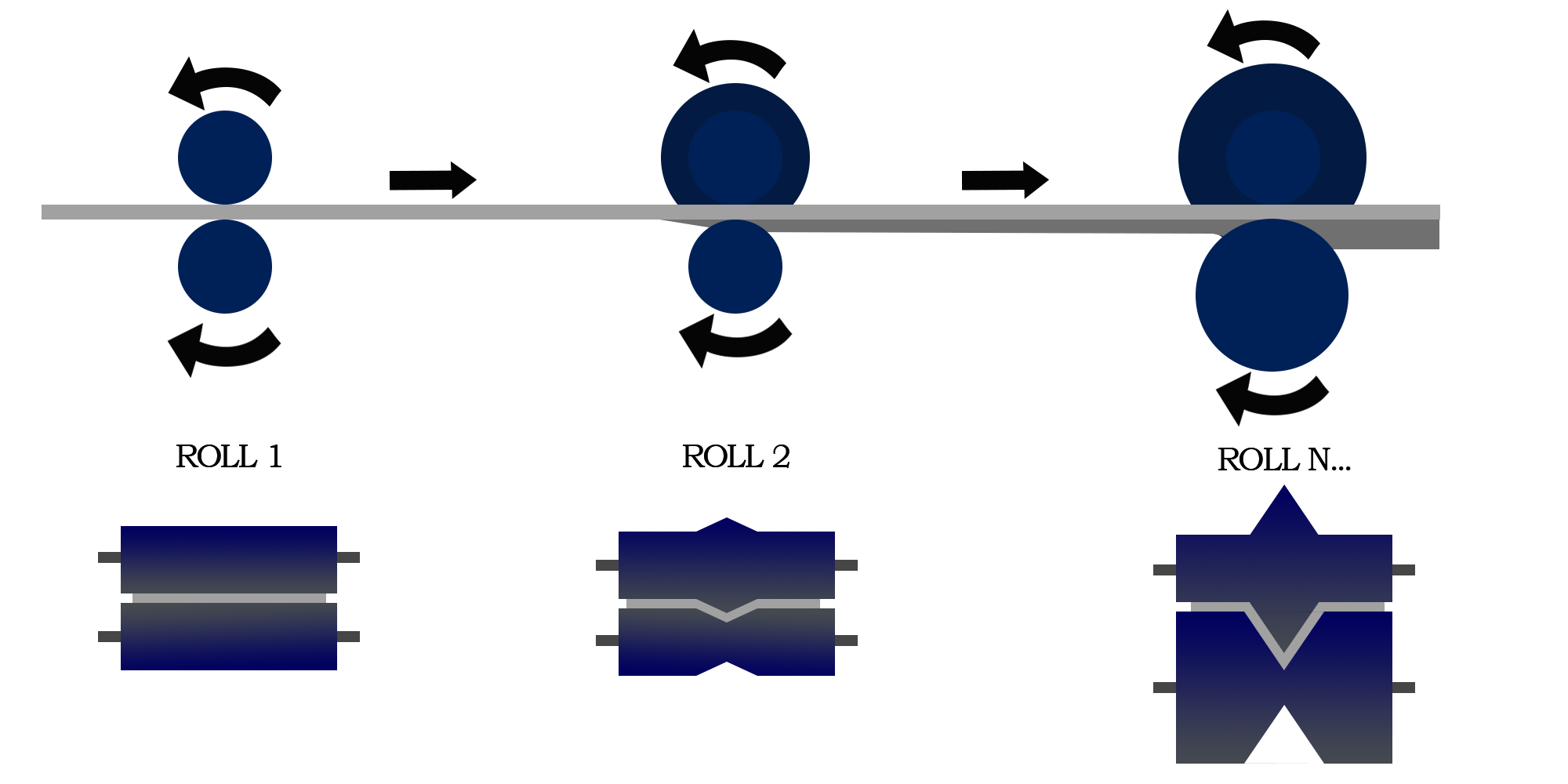
Advantages of cold roll forming
Cold roll forming produces lower residual stress in the metal than hot rolling, offering advantages for specific applications. Additionally, the controlled forming process minimizes surface imperfections and defects, leading to a polished final appearance.
Roll Forming Design Guidelines
When designing end products for roll forming, it’s important to consider both the desired shape and the processing limitations.
Factors to keep in mind include avoiding blind bends that are hard to control, using wide flanges to prevent breakage, and ensuring pre-punched holes are placed away from bend lines. Additionally, consider incorporating features like embossing and notching before or after the rolling process.
When it comes to shapes, be cautious of wide flat areas that may show imperfections in the material. Adding longitudinal ribs or edge formations can help compensate for these issues. Remember that metal thickness reductions can lead to control problems, so be mindful of corner radii to prevent pressure marks or metal fracture.
By following material bend properties and metal temper restrictions, you can design for successful roll forming with minimal maintenance needs.